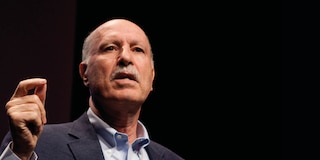
An interview with Yossi Sheffi (MIT)
“Covid-19 has elevated the role of supply chains”
About the expert
Dr. Yossi Sheffi is the Elisha Gray II Professor of Engineering Systems at the Massachusetts Institute of Technology, where he serves as Director of the MIT Center for Transportation and Logistics. He is an expert in systems optimization, risk analysis, and supply chain management, which are the subjects he teaches and researches at MIT. He is the author of many scientific publications and several books on supply chain management, resilience, and strategy. Dr. Sheffi has won several awards, including the Distinguished Service Award by the Council of Logistics Management, and the Salzberg Medal and Award for outstanding leadership and innovations in supply chain management.
Mecalux sat down with professor Yossi Sheffi, Director of the MIT Center for Transportation and Logistics, to talk about how Covid-19 is reshaping businesses and supply chains – and what’s coming next.
-
What are the key findings from your latest book The New (Ab)Normal: Reshaping Business and Supply Chain Strategy Beyond Covid-19?
Covid-19 has taught us several things about supply chains. First of all, we learned that the general media — including major publications in the U.S. and Europe — know very little about supply chains. The media tend to catastrophize everything.
-
How so?
Many media outlets reported that supply chains failed during the pandemic. Supply chains did not fail. In fact, it was the best time for supply chains. For instance, think about the food supply chain when Covid-19 hit: from one day to the next, all restaurants, universities, and industries were closed.
And yet supply chains adapted quickly to these abrupt changes in regulation and consumption patterns. The media made a big deal out of temporary small shortages, which were insignificant for the most part. By and large, nobody went hungry, and everything kept going. Supply chain executives, managers, and workers were the heroes of this pandemic.
“Covid has accelerated the adoption of technology and one of the main areas is robotics in warehousing”
-
In your book, you mention that by 2022 the worldwide market for warehouse and logistics robots will quadruple. How is Covid-19 accelerating automation in the supply chain and in warehouses?
Big time. Covid has accelerated significantly the adoption of technology and one of the main areas is robotics in warehousing. First of all, because robots don’t get Covid, don’t need to get vaccinated, and don’t have to wear a mask — they just work 24/7. Second, in the United States, now there are many more job openings than workers available. The current labor shortage is another drive for automation in general and, in particular, for robotics in warehousing. The thing with automation and robotics is not that it doesn’t make mistakes, but that you only make the mistake once. When you correct the algorithm, the mistake is fixed, and from this point forward, there’s no longer a problem.
-
How can businesses prepare for and manage disruptions?
Supply chain executives, managers, and workers were the heroes of this pandemic To begin with, you have to prioritize what you are preparing for. Most people think that you have to prepare for the things that are highly likely to happen. But, actually, the most dangerous thing that has to be prioritized is events that don’t happen often but have a significant impact. For instance, Covid-19, the BP explosion in the Gulf of Mexico, the nuclear power plant disaster in Japan … Who could have dreamed that Japan, the country that’s more prepared than any other, wouldn’t be prepared for earthquakes? It’s always easier to prepare for events that have happened before because you can drill them down and have the basic framework. But with events that have never happened before, you can only come up with general resilience.
-
What can you tell us about resilience?
Resilience is a concept taken from material science — the ability of a material to retain its shape after deformation. Here, we’re talking about the ability of a company to bounce back to the same level of service, manufacturing, and/or distribution after some kind of disruption. To prepare for disruption, you have to map your supply chain to know who the organizations upstream are. And, more than that, you have to overlay your bill-of-material on the geographic location so that, if a supplier is down, you know immediately which parts are not going to make it, which products you will not be able to build, and which of your customers you will not be able to supply. You have to prepare ahead of time and know what you will do if you cannot deliver everything to your customers and have to prioritize some customers over others. You also need to centralize all the information and the decision-making process to make sure decisions account for all the system-wide effects.
-
What doesn’t kill you makes you stronger.
A crisis is an opportunity to find out who the good customers, employees, and suppliers are. These are the people you should bet on coming out of the crisis. And you should think about whether you still want to have a certain division that didn’t perform or still want to deal with certain suppliers and customers. Crises are an opportunity to see who is committed to you in the long term.
-
Has Covid-19 brought positive opportunities for the supply chain?
One of the great things that happened is that Covid-19 elevated the role of supply chains. People used to ask my wife: “What does your husband do at MIT?” When she said I research and teach supply chain management, their response was: “What’s that?” Now, everybody realizes how important supply chains are. Their role has been elevated in companies, and more people are coming to the profession. Our program applications at MIT are increasing dramatically. People realize supply chain is a good career move because it controls everything that happens in the company: from the supplier to the transportation, to the manufacturing, to distribution, to returns.
Supply chain used to be just trucking and warehouses, a man’s work. Now we’re talking about computers, management, processes ... It’s become a very sophisticated profession. One of the metrics we see as a result of this is many more women joining the profession. This year we have 50-50 among our students, men and women. It’s great to see talent that was not even thinking about supply chain maybe 20 years ago turn to the profession. It can only make it better.
-
Any other positive learnings from Covid-19?
A mistake I see companies make sometimes is they buy technology without thinking about what problem they’re trying to solve The pandemic also triggered a much faster uptake of technology. Usually, it would take months or years for a company to make a decision to buy a piece of software. During the pandemic, the adoption of technology was done within weeks. The truth is that many companies felt that contracts were written so quickly that they needed a better legal review. Some companies now have committees that are looking at how they can do stuff quickly as they did during the first months of the pandemic, but without cutting too many corners.
-
Besides Covid-19, what other major challenges do businesses need to overcome in their supply chains?
Unfortunately, during Covid-19, we saw trade barriers and export restrictions for vaccines. Whenever there is a shortage and the demand goes up significantly, we’ll see countries that start to constrain how much can be exported out. This is bad news for chips in particular because users of these technologies are going up exponentially. The shortage of chips is a problem because it takes years to build a chip manufacturing plant and it’s a risky process. I was talking once to the CEO of one of the largest chip manufacturing companies about risks, and he said: “Let me tell you what risk means. Every few years, we dig a big hole in the ground and we put four billion dollars into it hoping that, a few years from now, it will make what we hope it will make. We don’t even know if science will be there yet, but we have to make the bet right now.” Talk about risk; that’s risk!
Another challenge in supply chain management is to understand the technology — it takes time to know where technologies such as blockchain or the Internet of Things fit and where they don’t fit. Some of the mistakes I see companies make sometimes is they buy technology without thinking about what problem they’re trying to solve.
-
When it comes to technology adoption, why are some companies more risk-averse than others?
There are companies that, in their DNA, develop experimental and risk-taking attitudes and others that are more risk-averse. Let me compare company X with company Y. Company X is a very successful and experimental company: when they develop a new product or software, they put it into production before it’s perfect and just wait for users to tell them what’s wrong to fix it. New ideas can go up in the organization and get approved quickly. Company Y, however, will never put something into production without quality assurance and lots of testing. Ten to fifteen years ago, company Y recognized the threat of company X and tried to emulate some of what Company X was doing, with limited success. It’s very difficult to change culture in fundamental ways.
-
What would a world without supply chains look like?
Without supply chains, trade wouldn’t exist. Supply chains enable trade because you bring something to somebody who needs it, so you have purchasing and distribution functions, even if it’s one person. All these elements were already present in the old Babylonian markets. Without supply chains, we would be back to every person for him or herself. We would have to hunt, build our own house, and do everything ourselves without taking anything from anybody. We would be back to the Stone Age. Supply chains enable the world to work; they are the invisible hand of the economy. Both buyers and sellers have an incentive to make it work. If the link between one buyer and one seller breaks, the seller will look for other buyers and vice versa. Supply chains don’t need major orchestration from above because every chain in the link has incentives to solve the problems as far as it can. The beauty of this is that there is no brain; you don’t need it. The system is the brain.