In recent years, there has been widespread change in the technology used to store electrical energy in automated handling systems. The largest manufacturers in the sector have been gradually replacing lead-acid batteries with lithium-ion batteries and supercapacitors since they maximise the performance of electric devices.
These new devices have been a breakthrough for materials handling systems in general and in particular for automatic systems. To better understand how thsi development has improved and evolved the market, first the characteristics of traditional batteries, such as lead-acid, must be given due consideration.
Lead-acid batteries
Batteries are composed of a repository of sulfuric acid where parallelly placed lead plates are submerged, alternated according to their polarity, and act as the cathode (negative pole) and anode (positive pole) of the battery. Inside the repository, a series of chemical reactions occur between the lead plates that allow the storage and extraction of electrical energy according to the needs of the device they are powering.
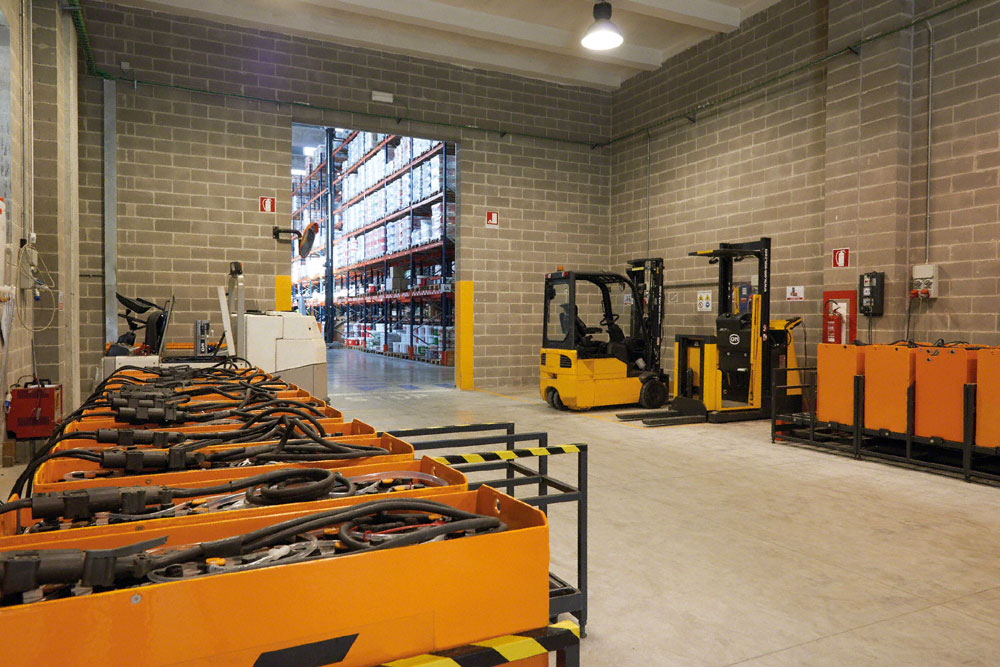
There is extensive worldwide use of these batteries due to the low cost per unit of stored electrical power (known as a low cost per watt-hour). In addition, they maintain the interior power levels very well while they are not in use.
The compartment where lead-acid batteries are recharged must be in a well-ventilated area away from storage areas and even be insulated
On the other hand, they only store a small amount of energy per unit weight or volume. Recharging them usually takes between 8 and 14 hours since the chemical reaction inside the battery must be slow to not prematurely degrade the storage capacity. Another downside is that during the process vapours and gases are emitted into the environment, which compels the allocation of a well-ventilated compartment for its usage.
The life of these batteries is approximately between 200 and 400 charge and discharge cycles, with deep-discharges advised against because they deteriorate and shorten its operating life. They also require maintenance to ensure the devices operate properly. Once its operating life is over, it is crucial to manage and process the materials, as they are highly contaminating.
In the past few decades, as a result of the increasing scarcity of petroleum, the industry has researched and developed new devices to reduce dependence on fossil fuels and minimise the emission of contaminating gases.
Here are two of the most advanced solutions:
Li-ion batteries (Li-ion)
The batteries employ a lithium-ion salt as an electrical conductor. There is a wide variety of Li-ion technologies depending on the materials used for the composition of the batteries' cathode and anode, such as iron phosphate, cobalt oxide, potassium oxide, etc.
This technology imparts numerous advantages to the industry due to its characteristics:
- High specific energy: more energy stored in power units that are smaller than lead-acid batteries.
- Increased energy efficiency: they heat up less and are more proficient than lead-acid when charging and discharging. The battery can charge and discharge with high intensity without degrading or deteriorating in only 3 or 4 hours. This feature makes them very suitable for equipment that must transport heavy loads at high speeds and accelerations.
- Long operational life: the battery life can be quadrupled when compared to traditional ones, depending on the particular lithium-ion technology.
- Non-contaminating: does not contain heavy metals or contaminants. Moreover, once its operational life is over it is not necessary to process them as toxic waste. They do not emit fumes during the charging process.
- No maintenance is required.
- Better performance at low temperatures: Li-ion technology can work in a very broad temperature range without degrading or its life is shortened.
The lithium-ion batteries provide high-performance in cold and frozen storage
However, it has some disadvantages:
- Electronic circuit protection: the components forming the batteries are safeguarded by an electronic circuit protection. That said, this also allows the device to know the status of the battery and thus optimise charging, discharging and its operational life.
- Charging at negative temperatures: the batteries cannot be charged below 0 °C. When they work in cold storage, it is essential to place the charging station outside the installation. Otherwise, the battery must be warmed during charging.
- Better watt-hour cost: : the cost per unit of stored energy is higher than lead-acid batteries. Nevertheless, this increased cost is offset by the long life of a Li-ion battery, which ends up reducing the total cost per cycle.
Supercapacitors
Also known as double-layer electrolytic capacitors, supercapacitors are devices that permit the storage of large amounts of energy, thousands of times greater than traditional capacitors.
Its many advantages include:
- High power capacity: they allow very high intensity charging and discharging without the premature degradation or deterioration of the battery. It can be charged in a matter of seconds.
- Very long life: the electronic components are highly durable. They can perform millions of charge and discharge cycles if kept in suitable work temperature conditions.
- Simple charging process: they do not require a specific charging curve and there is no risk of overcharging, unlike lead-acid batteries.
- Safety: there is no possibility of erosion or combustion due to supercapacitator overload or over-discharge.
- They are maintenance-free.
- Excellent performance at low temperatures: supercapacitors suffer minimal performance loss and do not degrade when working at low temperatures; in fact, the opposite happens, as its operating life is extended.
However, they have certain limitations:
- Low specific energy: supercapacitors can store a significant amount of energy, although not as much as traditional batteries of the same size and weight.
- Moderate self-discharge rate: they experience a greater spontaneous discharge process of electrical energy.
- High cost per watt-hour: the initial cost of supercapacitors is higher than traditional batteries. However, this cost is offset by its durability.
Batteries in the Mecalux Pallet Shuttle system
The incorporation of automatic or semiautomatic Pallet Shuttles in a warehouse is an ideal solution to increase productivity and profitability. It is highly recommended in installations with a large volume of pallets per SKU and a constant flow of incoming and outgoing goods.
Batteries are extracted from the shuttles and connected by simply fitting them into the charging stations set up in the warehouse
Both systems meet different needs: in the semi-automatic, an operator directs the movements of the shuttle via a Wi-Fi connected tablet after placing it in the corresponding channel with a forklift. Meanwhile, the automatic system is controlled by the warehouse management system (WMS) and assists the automated handling equipment (stacker cranes or transfer cars) to locate the shuttle and the load in the assigned channel. In both cases, the forklifts are not introduced into the storage aisles, reducing incidences and maintenance costs. The shuttle, driven by electric motors, moves through the inside of the channels with full autonomy to carry out the loading and unloading of the pallets. The semi-automatic version includes lithium-ion batteries and the automatic one contains supercapacitors. Let's look at their differences:
Lithium-ion battery in the semi-automatic Pallet Shuttle
The semi-automatic Pallet Shuttle system uses a lithium-ion battery as a power source.
Choosing a lithium-ion battery compared to the supercapacitor system is mainly due to the semi-automatic Pallet Shuttle's need for prolonged autonomy. These batteries are noted for their high specific energy, which can last up to 10 hours at maximum performance (depending on the characteristics of the warehouse).
This technology does not contain volatile metals, which provides an additional degree of safety and durability. It is composed of cells Li-ion iron phosphate interconnected in series and in parallel to provide a nominal voltage of 25.6 V and a storage capacity of 55 Ah.
This battery is custom designed for Mecalux since both its protectors and battery management are adjusted to the operating parameters of the semi-automatic Pallet Shuttle. This factor enhances the cells utility in the system.
Supercapacitors system in automatic Pallet Shuttle
The automatic Pallet Shuttle is equipped with a system of ultracapacitors as the main source of electrical power.
Supercapacitors are most suitable for the automatic system because they can recharge the power in seconds. Thus, the shuttles are always available and can operate continuously, 24 hours a day.
The automatic Pallet Shuttle moves between the different storage channels on board stacker cranes or transfer cars, where the power levels of the supercapacitors recharge during transfer.
When installing the automatic Pallet Shuttle system in a warehouse, there are two different options to choose from: the stacker crane or the transfer car
The system collects the electrical energy required for the loading and unloading cycles of 1,500 kg pallets in up to 45 m deep storage channels. The recharge time is variable depending on the depth of the channels and the weight of the load units (it may last only a few seconds in average length channels). Thus, high durability is ensured without any maintenance.