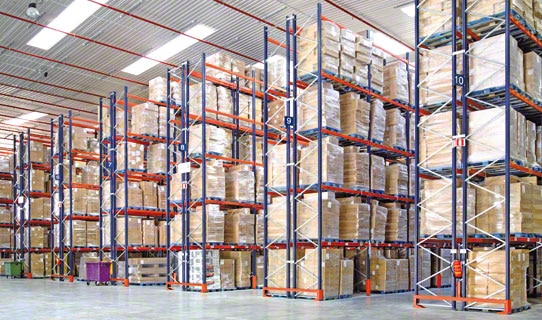
HAVI's three-temperature food storage system
HAVI's logistics centre in Lisbon, equipped with the latest Mecalux technologies, is made up of three warehouses that operate at different temperatures in order to efficiently supply customers in the catering sector.