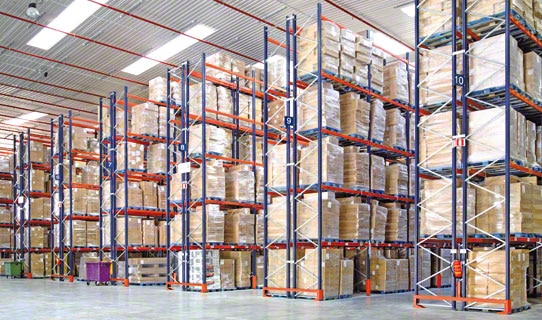
Würth Modyf adapts its logistics to omnichannel with the Easy WMS warehouse management system
How was Würth Modyf able to boost its growth and prepare over 1,500 orders a day during its peak season?
How was Würth Modyf able to boost its growth and prepare over 1,500 orders a day during its peak season?